What Is an Industrial Robot?
A Practical Guide for Today’s Manufacturers
Industrial robots have already changed manufacturing as we know it, but they're only getting started.
As of 2023, more than 4.2 million industrial robots have been deployed worldwide, and the International Federation of Robotics predicts continued expansion as demand rises across global supply chains. Industrial robot systems provide automation solutions for various industries, including the automotive industry, aerospace, supply chain logistics, and additive manufacturing.
At Melton Machine & Control Company, we provide a range of automated solutions, including robotic systems, for industrial applications. Learn more about these innovative systems from our experts below, or contact us today.
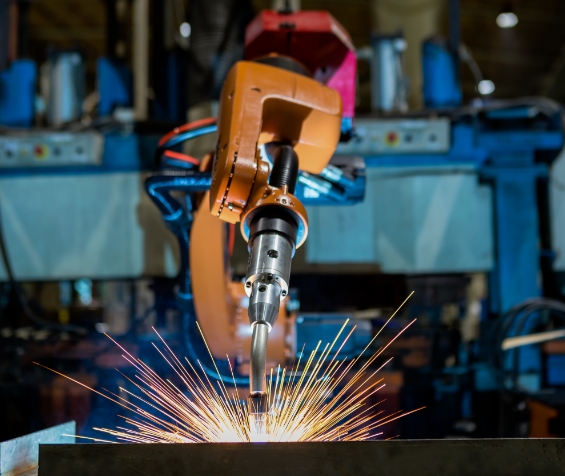
What are Industrial Robots?
Industrial robots are automated, programmable systems used in manufacturing to perform tasks such as welding, painting, assembly, and material handling. These sophisticated machines move on three axes—and often more—to complete tasks at high speed and with precision.
Robotic systems integrate advanced control platforms and various sensors for precise programming and operation, ensuring consistent performance. An industrial robot system can also excel at tasks requiring extreme endurance, reducing the need for human intervention in many repetitive or hazardous duties. Compared to other machines, robots offer greater flexibility and can adapt across multiple applications.
As artificial intelligence, machine learning, and automation technologies continue to advance, more companies are adopting robots to adapt to dynamic production needs and improve performance.
Humans and Robots Working Side by Side in an Industrial Environment
The growing use of industrial robots is reshaping the factory floor. While some roles may be automated, the shift is far from a simple case of job displacement. In fact, these technologies often improve worker safety, boost productivity, and enable companies to create new roles in robotics engineering, robot programming, and maintenance.
The rise of a more specialized technology, like collaborative robots, which are designed to safely work side by side with human workers, reflects a broader shift toward smarter, more integrated teams. As automation improves production efficiency and reduces costs, businesses can reinvest in upskilling their workforce.
Types of Robots
Traditional industrial robots began finding their place on factory floors in the 1960s, assisting in spot welding, die casting, and materials handling. Today’s industrial robots include a wide range of automated machines, each with unique characteristics and applications.
Every application comes with unique demands—including weight, reach, speed, three or more axes capabilities, and the ability to function in three dimensions. No matter what your production line needs, Melton aligns the right robotic system to your application.
Types of industrial robots include:
Collaborative Robots (Cobots)
Cobots are engineered to work side by side with humans and require minimal safeguarding. They perform tasks such as grinding, welding, and assembly while responding dynamically to their surroundings, making them ideal for high-mix production environments.
Autonomous Mobile Robots AGV
Mobile robots, including AGVs and AMRs, are designed for intralogistics and internal transport. Integrated with artificial intelligence and machine learning, they navigate around people and obstacles to optimize routes and support just-in-time delivery. These robots enhance agility in complex industrial environments.
Articulated Robots
These “robot arms” with multiple rotary joints—commonly six—enable complex motion paths and are widely used in welding, assembly, and tending tasks. They remain foundational across many sectors and are essential to Melton’s automation solutions.
SCARA Robots
SCARA robots are ideal for lateral movement and high-speed, precision-based jobs like electronics assembly and light-duty welding. Compact and reliable, they're commonly used in facilities with limited space or demanding production speeds for assembly and quality control automation applications.
Delta Robots
Delta robots offer rapid, lightweight movement and excel in packaging, small-parts assembly, and fast-paced production lines. Their ability to maintain precision while operating at high speed makes them valuable in industries like food, consumer goods, and pharmaceuticals.
Cylindrical & Polar (Spherical) Robots
These robots provide extended reach within compact work envelopes, ideal for injection molding, arc welding, and polishing. Though less common today, they remain effective for niche operations requiring cylindrical motion.
Artificial Intelligence in Robots
AI is enhancing robotic intelligence and autonomy across the industrial robotics sector.
With machine learning, robots can self-optimize paths, improve part recognition, and avoid downtime through predictive analytics. As robotics and AI converge, robotic systems will increasingly operate with minimal human intervention.
This means fewer programming errors, better product quality, and real-time adjustments to environmental changes. For manufacturers, AI brings reduced waste, faster throughput, and more agile responses to changing customer demand.
The Benefits of Industrial Robotics
From high-output production lines to precision assembly tasks, industrial robotics provides a measurable advantage across a wide range of applications. Whether you're scaling operations or solving for labor shortages, automation creates space for both growth and stability.
Some of the key benefits include:
- Shorter Cycle Times: Robots can work continuously without breaks, fatigue, or shift changes—accelerating production without sacrificing quality.
- Improved Safety: Automated systems take over repetitive or hazardous tasks, reducing the risk of injury and exposure for your human workers. Implementing standardized robots can also help you meet evolving safety standards in your industry.
- Consistent Quality: With exact programming and repeatable movements, robots help maintain uniformity across parts, reducing defects and rework.
- Greater Efficiency: Robotic systems are designed to minimize waste, reduce downtime, and streamline complex processes that might slow manual operations.
- Operational Flexibility: Many industrial robots can be reprogrammed or retooled to handle different tasks, making them valuable long-term assets in changing production environments.
- Scalable Solutions: From full robotic cells to collaborative cobots and autonomous mobile robots (AMRs), small to large companies can automate what matters most—whether it's one step or the entire line.
- Cost-Effective Growth: Smaller manufacturers can use robotics and other machines to automate high-impact bottlenecks without the overhead of full-scale systems, leveling the playing field.
Robotics brings precision, safety, and speed together to create an environment where your production line is more productive.
Challenges and Limitations: Integrating Your First Robot
High upfront costs, the need for operator training, and infrastructure upgrades can pose barriers, especially for smaller companies. Robotic systems may also require fine-tuning, troubleshooting, and IT resources to integrate with existing operations.
Yet with proper planning and the right automation expert by your side, the return on investment can be substantial. By supplementing human skills with robotic strength, companies create a more dynamic workforce and drive long-term efficiency.
The Future of Robotics for Industrial Applications
Looking ahead, robotics will continue to evolve. Advances in automation, AI, and sensing technology will unlock new industrial applications and push robots into roles beyond the factory floor.
Expect greater collaboration between humans and robots, enhanced by real-time data and intelligent software. As robotic technologies scale and diversify, companies embracing them now will be well-positioned to lead the next wave of digital manufacturing.
As always, Melton will be at the forefront of these evolving technologies. Continuing to provide one-of-a-kind automation solutions and robotic technology to revolutionize our clients’ operations.
Why Rely on Melton for Your Industrial Robot Needs
Melton combines engineering expertise, in-house fabrication, and trusted partnerships to deliver turnkey robotic systems built for performance. From collaborative robots and welding automation to material handling and custom integration, we tailor every solution to your unique production goals.
Our team ensures your robotic systems meet today's requirements while scaling for tomorrow. Whether you're just starting out or expanding your capabilities, Melton delivers solutions that are built to last.
Trust More Than 55 Years of Experience. Trust Melton.
Want to learn more about industrial robots and how they could fit into your existing workflows? Contact Melton today to get an assessment and speak with one of our experts.
START A CONVERSATION
Have questions? Want to submit an RFP to our experts? For more information or to start the journey toward your next automation project, reach out to Melton today. Our decades of expertise in automation can ensure your project’s success.